Carbon fiber parts require a very specialized process to manufacture. Metals like aluminum are forged in one piece and have isotropic strength (strong in every direction). Carbon fiber, however, has very different properties that need to be accounted for.
The first step is wet lay-up hand lamination. Watch the video to see this process in action!
Layup
Carbon fiber is a high-performance material that is used in many different applications. It has excellent stiffness and tensile strength as well as low thermal expansion. This makes it a better choice for manufacturing products than traditional materials such as metals and plastics.
When making a carbon fiber part, the first step is to layup the composite material. This involves applying a layer of carbon fiber fabric and wetting it with epoxy resin. This is done over a form, called a mold. The resulting product can then be used as part of the final component, Check out this site.
There are several ways to do this, including wet layup, pultrusion, prepreg layup, and infusion. Wet layup is the easiest and cheapest way to make a carbon fiber part, but it produces inconsistent physical properties and has a higher void content than other methods. Infusion is a more sophisticated process that ESE uses for its products because it provides consistent results with a very low void content and high fiber-to-resin ratio.
Prepreg
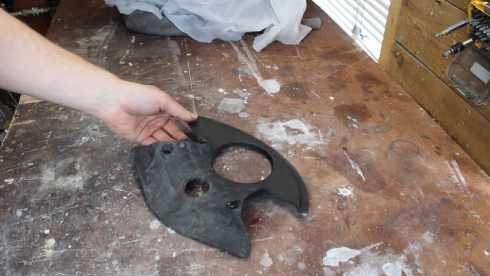
Carbon fiber is a versatile and efficient material for manufacturing high-performance lightweight products. Its tensile modulus is five times higher than steel, which translates into a very strong product at only a fraction of the weight.
A carbon fiber part can be fabricated using many different methods, depending on the type and size of the part, the design, and the desired properties. These include wet lay-up hand lamination, prepreg, and resin infusion.
Laying carbon fiber plies together to form a finished product is a skilled and labor-intensive process. This process is what allows carbon parts to achieve their outstanding strength, stiffness, and beauty.
The carbon fiber materials used in the layup process are known as prepregs, and they are impregnated with epoxy resin prior to molding. This resin provides protection and imparts the viscosity required to ensure fabric adherence to the mold surface. This is the process that is used to make the parts you see in this drone prop, and it produces a part with excellent tensile modulus.
Molding
There are a few different ways to mold carbon fiber. One popular process is called bladder molding. This process is ideal for companies creating hollow composite parts. It involves wrapping sheets of carbon fiber saturated with pre-preg resin around an inflatable bladder that is then placed inside a closed mold cavity and subjected to pressure. This causes the carbon fibers to bind together into the desired shape of the part.
Another carbon fiber molding technique is RTM. This method is more cost-effective than traditional CNC milling and is suitable for small production runs or for parts with complex shapes that cannot be produced using the negative molding techniques.
In this method, the carbon fiber fabric is laid over the mold and wetted with resin. The layup can be rolled, squeegeed, or vacuum bagged to remove air bubbles and help the resin bond to the carbon fiber fabrics. It is recommended to use a vacuum bag for this type of layup because it will help ensure the strength of the final product.
Curing
Carbon fibers are a stiff, lightweight material that is ideal for producing components that require high strength. This material is also very durable, with the ability to resist fatigue and vibration. It is often used in automotive components, like roofs, and visible parts such as the dashboard in the BMW i8.
To produce a carbon fiber part, you first need to make a mold. This can be done by hand or with a machine, depending on the size of the component. The best method is resin transfer molding, which is a more complex process that produces a better surface finish than hand layup.
Conclusion:
During the process, it is important to use protective equipment, such as goggles, gloves, and a face mask, to prevent inhalation of potentially harmful fumes. It is also recommended to work in a well-ventilated area. This helps reduce the risk of the formation of carbon monoxide. Then, the dry carbon fiber is placed in a male and female mold and resin is injected under high pressure.